Project Description
Definition of Aluminum Extrusion Molding
Aluminum extrusion molding is a kind of plastic processing method that applies strong pressure to the metal blank in the mold cavity (or cylinder), forces the metal blank to produce directional plastic deformation, and extrudes from the die hole, so as to obtain the required section shape and some mechanical properties of parts or semi-finished products.
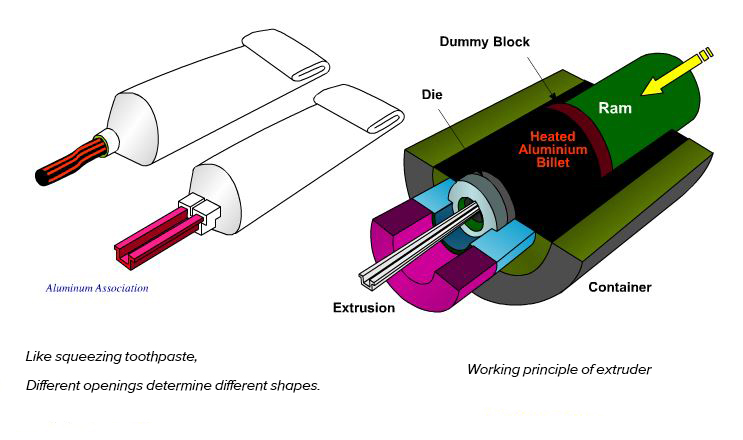
Classification of Aluminum Extrusion Molding
According to the flow direction of plastic metal change, extrusion can be divided into the following categories:
- Positive Extrusion: when producing, the direction of metal flow is the same as that of punch.
- Reverse Extrusion: in production, the direction of metal flow is opposite to that of punch.
- Compound Extrusion: during production, the flow direction of part of the blank is the same as that of the punch, and the flow direction of the other part is opposite to that of the punch.
- Radial Extrusion: during production, the direction of metal flow and the direction of punch motion is 90 degrees
Process Characteristics of Aluminum Extrusion Molding
- During the extrusion process, the extruded metal can obtain a more intense and uniform triaxial compression stress state in the deformation area than the rolling forging, which can give full play to the plasticity of the processed metal itself;
- Extrusion molding can not only produce bar, tube, type, and line products with simple section shape but also produce profiles and pipes with complex section shape;
- The flexibility of extrusion molding is large. Only the extrusion tools such as molds need to be replaced to produce products with different shapes, specifications, and varieties on one equipment.
- High precision of extrusion products, good surface quality of products, and improve the utilization rate and yield of metal materials;
- The extrusion process has a good effect on the mechanical properties of the metal;
- The short technological process, convenient production, single extrusion or larger overall structure parts with a larger area than hot die forging or molding and rolling, low equipment investment, low mold cost, and high economic efficiency;
- Aluminum alloy has good extrusion characteristics and is especially suitable for extrusion processing. It can be processed through various extrusion processes and various die structures.
Advantages of Aluminum Extrusion Molding
- Improve the deformation capacity of aluminum.Aluminum is in a strong three – way compressive stress state in the deformation zone.
- High comprehensive quality of products. Extrusion molding can improve the structure and mechanical properties of aluminum. After quenching and aging, mechanical properties of longitudinal (extrusion direction) of extruded products are much higher than those of similar products produced by other processing methods. Compared with rolling, forging and other processing methods, extrusion products have high dimensional accuracy and good surface quality.
- Wide range of products. Extrusion can not only production profile is simple tube, rod, wire, and can also produce the section shape is very complex, solid and hollow profile products section along the length direction of the phase change and gradual change of variable cross-section profiles, many of the products in the shape of a cross section is beyond the forming of other plastic processing methods. The size range of extruded products is also very wide, ranging from the extra-large pipe and profile with a diameter of 500-1000mm to the ultra-small precision profile with the size of matchstick.
- Great flexibility in production. Extrusion molding has great flexibility. It can produce products of different shapes, sizes, specifications and varieties on the same equipment with only changing molds. Besides, the operation of changing moulds is simple, convenient, time consuming and efficient.
- Simple process and less equipment investment. Compared with pipe and profile production processes such as perforated rolling and groove rolling, extrusion molding has the advantages of short technological process, less equipment quantity and less investment.
Disadvantages of Aluminum Extrusion Molding
- Uneven tissue performance of products. Because the flow of metal is not uniform during extrusion (especially serious when there is no lubricating forward extrusion), the surface layer, center, head and tail of the extrusion products are not uniform.
- The working conditions of the extrusion die are harsh and easy to worn out. During extrusion, the blank is in a nearly closed state with high three-way pressure. At the same time, the mold is usually subjected to high temperature and high friction during hot extrusion, which greatly affects the strength and service life of the mold.
- Low production efficiency. In addition to the continuous extrusion method developed in recent years, the conventional extrusion methods can not achieve continuous production. Generally, the extrusion speed is much lower than the rolling speed, and the geometrical waste loss and yield of the extrusion production are low.
Summary
In recent years, due to the pursuit of miniaturization and lightweight in various industries, the aluminum profile has been widely used in construction, transportation, electronic appliances, aerospace, and other industries. As a result, the proportion of aluminum extruded products has also increased rapidly.