Project Description
What is black anodising?
Anodising is a treatment process in which an oxide film is formed on the surface of the metal by an electrolytic oxidation reaction. In this process, the metal or alloy part is used as an anode to form an oxide film with protective, decorative and other functional properties on its surface by the action of an applied electric current under specific electrolyte and process conditions.
Black anodising is the electrochemical process of darkening aluminium parts by first performing standard anodising to form a semi-porous aluminium oxide layer. The oxide layer is then dyed black using one of the three dyeing techniques: organic dyes, inorganic dyes or electrolytic dyeing of metal salts.
Metals that can be black anodised are aluminium, magnesium and titanium, of which aluminium is the most commonly used for black anodising, but not all grades of aluminium can be black anodised, only the alloy 5000 series, alloy 6000 series and alloy 7000 series of aluminium can.
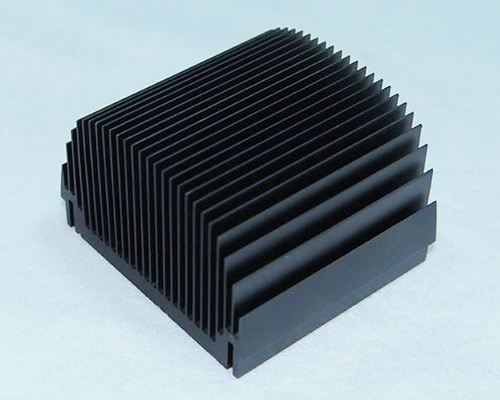
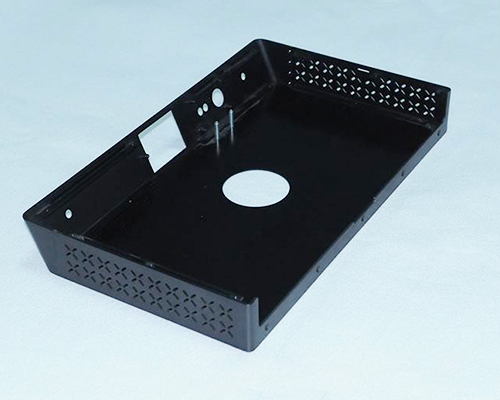
How does black anodising work?
Black anodising works by first anodising the part using the standard anodising process and the Type II or Type III anodising process. For optimum colour fastness, a minimum thickness of 25 microns or more is recommended for the anodised coating. After anodising, the part will have a semi-porous surface structure and these pores are used to accommodate the black dye. There are three dyeing techniques:
- Organic pigments:
Organic dyes are dissolved in warm water and placed in a dye bath, followed by the part, and the dye will fill the semi-porous surface of the anodic layer. Typically, black dyeing requires additional dyeing time compared to lighter colours. Organic dyed parts are not recommended for outdoor use.
- Inorganic pigments:
These pigments are insoluble in water and the coatings they produce have excellent lightfastness. For black anodising, parts can be produced using cobalt sulphide inorganic salts.
- Electrolytic Staining:
After standard anodising, the part is placed in another electrolytic tank containing a solution of heavy metal salts. The anode layer acts as the cathode and the stainless steel electrodes are placed in an acidic electrolyte bath where the metal salts will then be deposited to the bottom of the holes. Nickel, cobalt and tin salts are used to produce different colours, a proprietary process that produces parts with superior colour fastness.
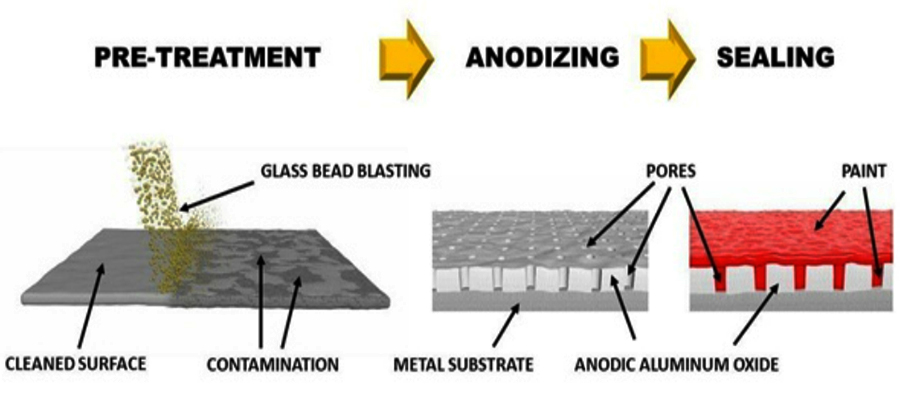
After dyeing, the pores in the anode layer must be sealed to prevent colour leaching. The sealing is usually done by hydration, which closes the pores by reacting with the anode layer, or by implementing a chemical seal, e.g. through the use of nickel acetate or dichromate seals.
The time required to black anodize the part depends on the desired anode layer thickness, the dyeing method and the post-dye sealing technique. Generally, anodising 2.5 microns takes 5 minutes. Therefore, the minimum black anodising thickness recommended for anodising is 25 microns, which takes approximately one hour, and the dyeing process may take up to 20 minutes, moveover, these timeframes are also dependent on the cleaning and rinsing process.
Black anodising applications
- Home appliance field: commonly used in home appliance shells, handles and other parts, to improve the texture and grade of the product.
- Automotive field: widely used in automotive parts, such as wheels, body trim, etc., to increase the sense of fashion and luxury car appearance.
- Electronic field: commonly used in mobile phones, tablet PCs and other electronic products on the shell and keys, to improve the texture and durability of the product.
- Architectural field: it can be used on building curtain walls, doors, windows, ceilings and other components to increase the modern and artistic sense of the building.
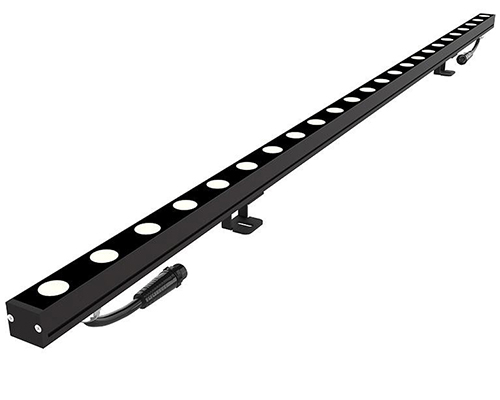
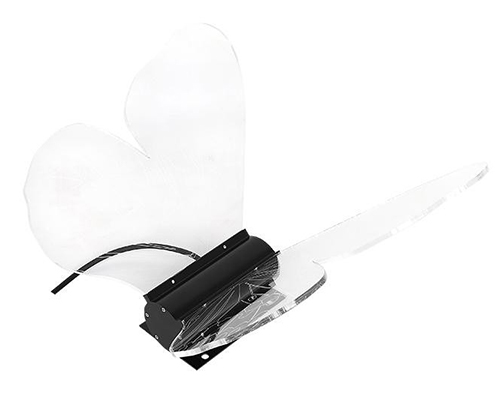
In addition, black anodized aluminium has a wide range of applications in other industrial fields such as the aviation manufacturing industry and the automotive industry, such as improving the hardness and wear-resistant properties of aircraft parts, as well as improving the surface hardness and anti-corrosion properties of automotive parts.
Advantages of black anodized surface treatment
The benefits of black anodizing include improved wear and corrosion resistance, and this finish ensures that anodized aluminum components are less prone to rust. Rust is often used to describe the formation of a destructive flaking oxide layer on ferrous metals, and when an oxide layer forms on aluminium, it adheres to the surface of the metal and prevents further oxidation of the substrate.
In addition, black anodising has some additional specific benefits:
- Thermal Emissivity: Aluminium components are often dyed black to increase their emissivity and applications can include heat sinks as well as satellite components.
- No outgassing: Black anodised parts, if properly sealed after dyeing, will not outgas when exposed to a vacuum, and the lack of outgassing helps to protect sensitive equipment.
- Colour fastness: Black anodised parts, especially when dyed with inorganic or metallic salts, have excellent colour fastness, meaning they will generally retain their colour when exposed to UV (ultraviolet) light.
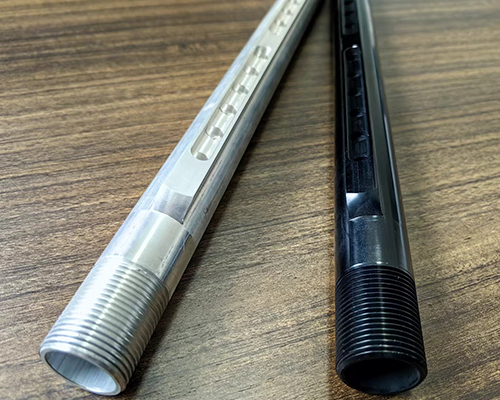
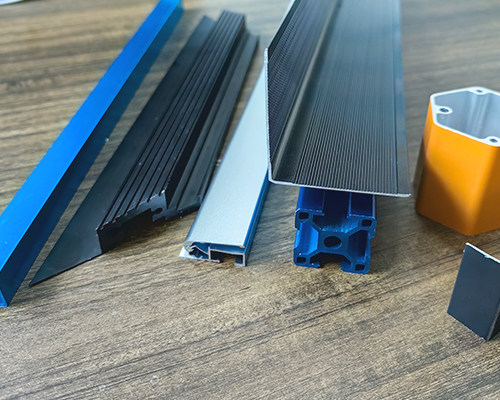
Limitations of black anodising
While black anodising is a robust finishing process with significant advantages, it also has limitations:
- Surface cracks: When exposed to thermal cycling, black anodised parts can form cracks in the anodic coating, which are mainly due to the difference in thermal expansion rates between the substrate and the coating.
- Limited Materials: Not all aluminium series can be black anodised. In general, the most common anodised aluminium series are 5000, 6000 and 7000, with 6000 being the most common anodised series.
- Fading: If organic dyes are used, black anodised parts will tend to fade as they are not suitable for UV exposure.
Although black anodising has a wide range of applications and many advantages, it is necessary to pay attention to its possible shortcomings in the process of application in order to take appropriate measures for prevention and treatment. If you have a need for black anodising of aluminium parts or a related problem, please remember to contact us!