Project Description
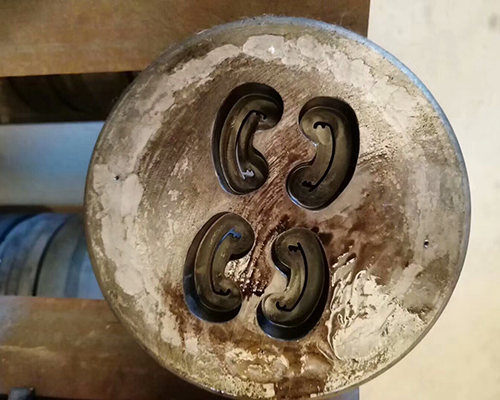
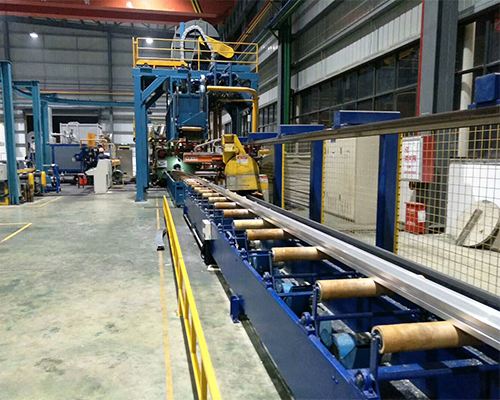
Currently, the main aluminium alloy is 6061, 6063 and 6063A with high-temperature extrusion, rapid cooling and artificial aging T5 (or solution heat treatment T6). Then carries on the surface treatment such as anodized & dye, electroscopic coating, powder coating and PVDF coating.
Alloy 6063 chemical element content range is wide. Due to the different roles played by various elements in the alloy, it is necessary to consider the content of each element in the alloy and the collocation of relationship between each other, which ensure the ideal performance of alloy and good economic benefits.
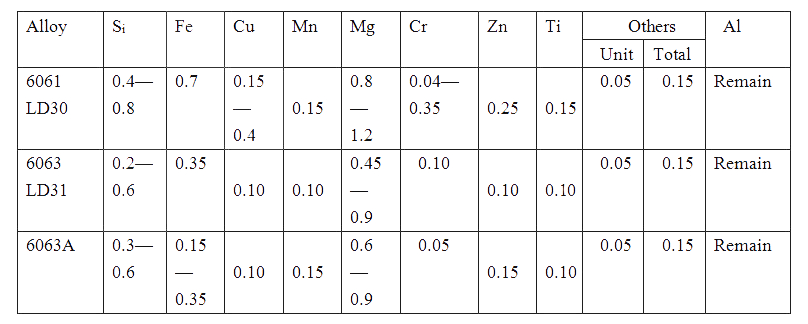
The main alloy elements are Mg and Si, and the main strengthening element is Mg2Si. To ensure Mg2Si is fully dissolved, and the amount of Mg2Si in the alloy are not less than 0.75%. But the solubility of Mg2Si is connected with the content of Mg in the alloy, the mass ratio between Mg and Si in Mg2Si is 1.73:1, if Mg2/Si > 1.73, Mg is surplus, the excess of Mg will significantly lower solubility of Mg2Si in solid aluminium alloy and weaken the effect of strengthening; if Mg2/Si < 1.73, Si is surplus, the excess of Si has little impact on solubility of Mg2Si and basically not weaken the effect of strengthening.
Fe is one of the largest elements impacts on the quality of anodizing & dye. With the increase of Fe, the anodizing film is glossed dark and transparency reduced, the radiance and brightness of aluminium alloy profile will visibly reduce and impair body appearance as well. So, highly Fe element content is not easy to anodize & dye.
In addition, because that the chemical compound formed by Fe and Si has strong thermoplastic and easily makes casting crack. Especially when the contents Fe<Si, it is easy to form ternary eutectic of low melting point and more hot brittleness on the grain boundary. While the contents Fe>Si, it will release peritectic reaction of the high melting point which improves the brittleness of temperature limit and in turn reduce the tendency of cracking.
Therefore, we should first of all control well the contents of Mg, Si and Fe elements and the mutual relation of them, not only ensure form enough hardening constituent Mg2Si in the alloy, but also guarantee that there is a certain amount of Si excess that is less than the content of Fe element, and more the content of Fe in the alloy does not affect the quality of anodizing & dye. Like this, the alloy has a certain intensity, lowers the crack tendency, and meantime the quality of anodizing & dye is not reduced.