Project Description
Refer to surface treatment of aluminium profiles, there are Polishing, Anodizing, Powder Coating etc. these are commonly used. Today we will talk about Powder Coating.
The manufacture of the fixture and the choice of feeding method. The fixture placed at both ends should ensure that it can withstand a considerable weight of pressure; the use of the fixture in the middle of the use and production process should be used to minimize the fixture and profile of the outer surface of the contact point size, and should be placed on the vertical Pole part of the bucket powder. The placement of the stencil in the profile should also follow appropriate principle. For some of the deep groove profile, increase the amount of powder and push the distance between the claws and profiles are applicable. Surface area is large or complex structure should be prohibited to put in the downward position, but also to distinguish between the decorative surface and non-decorative surface.
For some special shape of the profile, timely adjustment of the fixture position, so that profiles in the hanging position to maintain a certain tilt angle to enhance the smooth running process, easy to powder adsorption. Also for some of the heavier profiles in the use of the middle of the fixture, the elbow should be part of a certain degree of curvature, the curvature of the fixture can ensure that the profile in the vertical position to ensure the smooth production process. In addition, the conductive beam and hanging with the increase in the number of recycling, the film will accumulate more. The coating itself is nonconductive and affects the conductivity of the conductive beam and the hook, which in turn affects the uniform distribution of the powder on the surface of the profile. The coating on the conductive beam and the hook should be selected in a suitable manner.
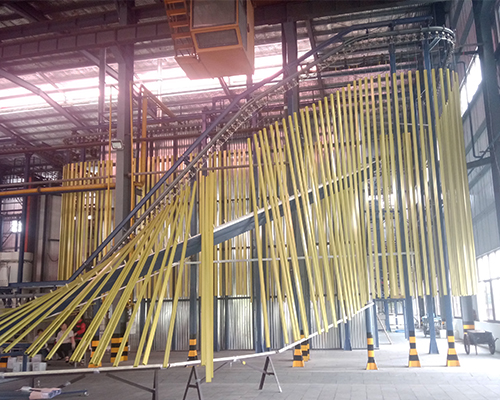
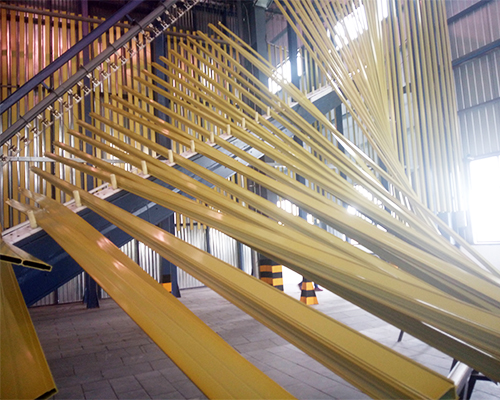
Pretreatment process than the ordinary pre-oxidation process is simple, mainly for degreasing and chrome, low consumption of raw materials, routine maintenance work is relatively easy. Pre-treatment process in order to improve production efficiency, and reduce the energy consumption in the drying process, the use of the larger rack, as much as possible to deal with the profile. For some of the soft texture of the profile, should be more in the middle of the profile placed crossbar, so that part of the groove as far as possible placed, is conducive to the evaporation of water. When the drying process is completed, there is still water residue, in order to avoid damage to the surface of the profile of the film and the temperature is too high when the profile is easy to produce deformation, should not be replaced in the furnace baking, can be used dry or air gun (No oil and gas) dry way. In addition to the profile of the trough and in the drip process, must maintain the appropriate tilt angle, but likely to cause part of the profile slip, should be used at the end of a part of the end of a piece of stainless steel wire mesh as a precautionary measure.
The problem should be noted in the spray. Formal spray before, you can try to spray a few times, then at both ends of the spray can observe the size of powder and powder distribution of the uniformity. The powder at this time within 10cm from the end of the jaw head part of the line running, the other part is the form of atomized powder, adsorption on the surface of the powder is actually the effect of this powder, the existence of such atomization The effect of the powder is to control the distance between the spray claw and the standard of the standard.